In today’s fast-paced business environment, time is a precious commodity, particularly when it comes to producing essential business material printing. It may come as a surprise that the process of folder printing can be rather time-consuming. This is not due to inefficiency but is reflective of a complex process that includes meticulous planning, designing, and quality assurance to deliver a product that upholds professional standards. Understanding the nuts and bolts behind folder printing delays and the requisite print production time is vital for businesses investing in their marketing collateral.
Frequent printer reboots or reconnections highlight the operational challenges, with as many as 25% of print jobs affected by connectivity issues. This, combined with unanticipated configuration errors and settings adjustments that encompass another 27% of user-reported issues, punctuate the nuances of print optimisation. To further elucidate the intricacies of folder printing, we encourage you to peruse a comprehensive printing guide, which offers a wealth of knowledge and insightful tips.
Common misconceptions may lead some to believe that faster printing equates to lower quality. However, the data speaks a different story. With a staggering 40% of issues stemming from improper setup, it’s clear that rushing the process could compromise the seamless interaction between software and printer drivers, integral to achieving high-quality folder prints.
Key Takeaways
- Quality business material printing involves a strategic process with several stages that can lengthen folder printing delays.
- Print production time is impacted by printer status issues, affecting around 25% of print tasks.
- Configuration and printer settings irregularities form a significant portion of printing woes, underscoring the importance of robust user controls.
- Resources like an in-depth printing guide can be invaluable in navigating the folder printing venture.
- Efficiency in printing should not compromise quality; proper setup and calibration are key to high-quality output.
Understanding the Folder Printing Process
The journey of creating customised folders encompasses a blend of art and science, ensuring that every aspect from design to delivery upholds the highest standards of quality and precision. This meticulous process is vital not only for achieving aesthetic appeal but also for maintaining functional utility across varied uses.
What is Folder Printing?
Folder printing refers to the custom creation of folders used primarily for business presentations or organisational purposes. The design and manufacturing involve a detailed selection of materials and printing techniques aimed at producing durable and visually appealing products. These folders, whether used for filing important documents or distributing marketing materials, play a crucial role in corporate branding and professional presentations enhancing design precision.
The Stages Involved in Production
The production stages of folder printing are comprehensive, starting from the initial conceptualisation to the final output. Each step is monitored to ensure adherence to the prescribed specifications and client expectations. Here’s a simplified breakdown of these stages:
- Design & Artwork Creation
- Material Selection
- Printing
- Finishing Techniques (e.g., laminating, folding)
- Quality Assurance & Packaging
Importance of Precision in Design
Design precision is paramount in folder printing, as it directly impacts both the usability and brand perception. This requires a sharp attention to detail in every aspect of the folder’s design, from ensuring consistency in brand colours to the strategic placement of pockets and card holders. Employing advanced design techniques not only enhances the folder’s aesthetic but also its functionality, making it a potent tool for effective communication.
Type of Folder | Price | Size | Thickness (points) |
---|---|---|---|
Standard Presentation (Two-Pocket) | $0.19 each | 9×12 inches | 10 |
Legal-Size Presentation | $0.59 each | 9×14 inches | 12 |
Certificate Presentation | $0.14 each | Customised for certificates | Varies |
Mini Presentation | $0.19 each | Smaller than 9×12 inches | 10 |
To further explore the complexities of folder printing and to gain insights into designing high-quality presentation folders, delve into the helpful resources provided by Printivity. Here, you will find valuable tips and information on enhancing your project’s visual and practical appeal.
Factors Influencing Printing Time
The duration required to produce high-quality printed materials can vary significantly due to several critical factors. Each element from material selection to the volume of print jobs considerably influences overall efficiency and output timelines.
Material Selection and Its Impact
Choosing the right printing materials is pivotal. High-quality papers ensure better adhesion and less wear on printing machinery, which directly improves print technology efficiency. For instance, using low-quality paper can lead to problems like ink smudging, which then requires additional time for reprinting. It’s essential to select materials that complement the technology in use to optimise both time and quality.
Print Technology and Equipment Speed
Advancements in print technology continue to revolutionise how quickly printing tasks can be completed. High-efficiency printers and the integration of automated systems reduce the time needed for large print runs, substantially enhancing productivity. Factors such as the operational speed of a laser printer and its handling of different materials play a crucial role in determining the pacing of print operations.
Volume of Print Jobs
The order volume impact on a printing business’s operation is substantial. High volumes can lead to longer queues and increased wait times unless managed efficiently. Businesses that balance their workload with high-speed, high-quality printers generally maintain more consistent turnaround times, even when handling larger orders.
In summary, by understanding the influence of materials, technological capabilities, and job volume, printing businesses can make informed adjustments to minimise delays and optimise printing time. These adjustments not only enhance operational functionality but also ensure client satisfaction through timely deliverables.
Design Complexity and its Role
The interplay between design complexity and printing timelines is pivotal, particularly when exploring the realms of custom folder design. It’s not merely about aesthetics; the complexity determines the pace at which designs become tangible products. This section delves into how different design choices impact the workflow, focusing on custom designs versus standard templates and the consequent artwork setup and design approval processes.
Custom Designs vs. Standard Templates
Opting for a custom folder design inherently involves a more intricate artwork setup process. Unlike standard templates which are pre-designed and can be quickly adapted, custom designs require starting from a blank slate, demanding input from both the designer and the client to meet specific aesthetic and functional criteria. This personalised approach not only enhances brand identity but significantly extends the timeframe for the design approval process due to the iterations required to finalise the artwork.
File Preparation and Artwork Approval
The artwork setup for custom folder designs often encompasses various phases of drafts and revisions which necessitate robust collaboration between the design team and the client. To streamline the design approval process, it’s crucial to understand and implement efficient file preparation practices. This involves using the correct file formats, ensuring high-resolution graphics, and aligning the design elements with the printing specifications.
Design Aspect | Custom Design | Standard Template |
---|---|---|
Time for Initial Concept | Several Days to Weeks | Hours to Days |
Artwork Setup | Complex; Tailored to Brand | Minimal; Pre-defined layouts |
Design Approval Time | Extended with Revisions | Quick with Few Changes |
Overall Impact on Timeline | Increased | Reduced |
The decision between custom designs and standard templates affects not just the visual uniqueness of the folders, but drastically alters the lead time due to the different levels of complexity in design preparation and approval. Understanding these distinctions helps in managing expectations and aligning delivery timelines with business needs.
Quality Control Processes
In the realm of folder printing, maintaining meticulous quality assurance standards is imperative to ensure that the final products meet client expectations accurately. The quality control phase is pivotal in capturing any potential issues that could lead to production delays or compromised product quality.
Importance of Proofing Before Final Print
Proofing is one of the essential proofing processes in printing. It involves the critical examination of a pre-production sample or a digital proof. This step is vital because it ensures that any discrepancies can be corrected before the mass production begins, safeguarding against costly errors and ensuring high-quality output.
Consider statistical insights like companies using tools such as Oracle Enterprise Data Quality to assess the completeness and consistency of data, ensuring that the proofs are impeccable. Emphasizing accuracy during proofing aligns with quality dimensions that advocate for timeliness and consistency. Regularly employing these strategies can dramatically decrease the instances of reprinting, thus avoiding additional costs and time delays.
Common Reasons for Production Delays
The causes of production delay causes are multifaceted, often stemming from quality control issues identified during proofing. Software glitches like ‘Configuration Parser Error’ or hardware malfunctions such as ‘Access violation, WINSPOOL.DRV error’ can halt production, requiring immediate technical resolutions to prevent extensive delays.
Data from sectors with implemented Total Quality Control (TQC) and Just-In-Time (JIT) production shows significant defect reduction in a short time, underscoring the effectiveness of rigorous quality control systems. For instance, adopting systematic approaches to quality management helped a machine shop reduce defects from 20% to 2% within just three months, directly impacting their operational efficiency and reducing production delays significantly.
To conclude, integrating advanced quality assurance frameworks and proofing processes in the folder printing industry not only reduces the risk of production delays but also enhances the overall product quality. By understanding and implementing rigorous proofing and problem-identification methods, businesses can ensure smoother operations and higher customer satisfaction.
Printing Materials Used
Delving into the materials utilised in the printing process, it becomes apparent how significant the choice of paper types, printing timing, and coating effects can influence the overall speed and efficiency of production.
Types of Paper and Their Effect on Timing
Selecting the right paper stock is not only a matter of quality but also impacts the printing timing. Papers with higher grammage, such as 350 gsm Matt and Gloss, generally require more time for printing and drying. This is contrasted with lighter papers like the 80 gsm Bond, which are quicker to handle and dry faster, streamlining the printing process.
Coatings and Finishes: Do They Delay Printing?
While coatings such as lamination add a desirable finish and durability to printed materials, they necessitate additional processing time. The curing period for UV coatings or the setting time for varnishes can extend overall production timelines. However, these finishing touches are crucial for enhancing the aesthetic appeal and functional longevity of the printed folders.
Paper Type | Grammage | Typical Use | Coating Options | Impact on Printing Timing |
---|---|---|---|---|
Standard Matt | 100 gsm | Mass distribution flyers | Lamination | Medium |
High-Quality Gloss | 350 gsm | Premium presentation folders | UV Coating | High |
Bond | 80 gsm | Business forms | None | Low |
The Impact of Quantity on Printing Time
The number of folders requested in a print order profoundly affects the overall printing duration. Understanding how different print order quantities influence time can help streamline the decision-making process and forecast the production schedule more accurately.
Small Runs vs. Bulk Orders
Opting for small vs. bulk printing can present unique challenges and benefits. Small print runs, often favoured by businesses testing a new market or design, can be processed quickly. However, the setup time per piece might increment the total production cost and time inefficiently. On the other hand, bulk orders, while requiring a significant initial setup, utilise economies of scale, making them less expensive per unit and more time-efficient overall once the print run begins.
To further understand the nuances between small and large print order quantities, one can explore detailed insights on printing techniques that handle various demands efficiently.
Running Multiple Designs
The complexity scales when handling multiple design handling within a single print order. Unlike a uniform batch, multiple designs require additional setup for each variation, potentially increasing the print timeline. Production scheduling must account for this to avoid delays, especially in scenarios where sequential printing is the only option.
When considering large-scale projects or specialised orders, enlisting expertise in efficient design handling techniques becomes beneficial. Comprehensive planning ensures all designs are accurately aligned with print specifications, as miscommunication or errors can extend downtime and affect overall delivery.
Here is a concise summary of how print order quantity can impact folder printing times:
Feature | Small Print Runs | Bulk Printing | Multiple Designs |
---|---|---|---|
Setup Time | Higher per unit | One-time setup, less per unit | High, varies by design |
Cost Efficiency | Lower | Higher | Depends on similarities between designs |
Time Efficiency | Less Time Efficient | More Time Efficient | Less, depends on sequential or simultaneous capability |
Best Use Case | Testing new designs/markets | Established products at scale | Varied product lines or targeted campaigns |
Thus, effectively managing print order quantity, small vs. bulk printing, and multiple design handling becomes pivotal in balancing cost, time, and quality in folder printing services.
Delivery and Logistics Considerations
When considering the end-to-end process of folder printing, understanding the complexities associated with folder delivery logistics is crucial. The effectiveness of the delivery methods directly impacts the overall customer satisfaction and efficiency of service. Below, we delve into the different shipping options, their timeframes, and the inherent delivery challenges in both local and international contexts.
Shipping Options and Their Timeframes
Choosing the right shipping option is pivotal in managing shipping timeframes effectively. Local delivery options often promise quicker turnaround times due to shorter distances and fewer logistical hurdles. On the other hand, international shipping requires navigating through various regulatory and customs clearances, which can extend delivery schedules significantly. It is important for businesses to align their delivery strategies with customer expectations and project timelines.
Local vs. International Delivery Challenges
While local deliveries can be straightforward, international folder delivery logistics encompass a broader spectrum of challenges. The complexities increase with the necessity for compliance with international trade laws, customs documentation, and adjusting to the logistical capacities of the destination country. Not only does this affect timelines, but it also adds layers of bureaucracy that can affect the fluidity of delivery schedules. Reliance on physical paperwork in many international settings further complicates the process.
To enhance the efficiency of these processes, integrating digital automation within delivery logistics can drastically reduce delays and improve accuracy. Automating crucial documentation, such as the Bill of Lading, airway bills, and custom forms, can streamline operations and optimise delivery outcomes significantly.
Logistical Factor | Impact on Delivery Schedules |
---|---|
Customs Clearance | Can extend international shipping by several days |
Digital Documentation | Reduces processing time and minimises errors |
Local vs International Regulations | Varying standards can necessitate additional compliance time |
Physical Paperwork Reliance | Increases risk of delays and document misplacement |
Understanding these elements within folder delivery logistics helps businesses and customers alike to navigate the potential pitfalls and streamline their operations. By focusing on enhancing digital capabilities and choosing the right shipping options, companies can ensure more reliable and efficient delivery frameworks, crucial for achieving satisfaction and operational success in the competitive market of folder printing.
Customer Collaboration and Feedback
In the realm of folder printing, the synergy between customer collaboration and effective communication in printing plays a pivotal role in achieving timely and successful project completions. It is essential to establish a foundation where feedback is not only encouraged but also seamlessly integrated to optimise production processes and reduce potential delays.
Importance of Timely Communication
Studies demonstrate that clear communication in printing projects significantly lowers the number of revisions needed, with effective customer collaboration potentially decreasing revision cycles by 20-40%. This reduction is crucial as approximately 80% of project delays are rooted in miscommunication among stakeholders. Regular updates and the use of advanced cloud-based solutions, such as Google Workspace or Microsoft OneDrive, have shown a 30% boost in productivity compared to traditional file-sharing methods.
Addressing Concerns and Adjustments
The process of integrating feedback implementation must be structured to ensure that every piece of input adds value to the project. For instance, designated feedback protocols can reduce wasted time by 30%, enhancing efficiency and stakeholder satisfaction by 20%. Implementing a well-defined file naming convention can also accelerate file retrieval times by up to 40%, further streamlining workflow and improving project turnaround times.
Table illustrating the impact of communication tools and protocols on folder printing projects:
Communication Tool/Protocol | Improvement in Productivity | Reduction in Revision Cycles | Increase in Stakeholder Satisfaction |
---|---|---|---|
Cloud-based solutions (e.g., Google Workspace) | 30% | Not directly applicable | Not directly applicable |
Designated feedback processes | Not directly applicable | 30% | 20% |
Clear file naming conventions | Efficiency in workflow | Not directly applicable | Not directly applicable |
In conclusion, cultivating robust mechanisms for customer collaboration and feedback implementation not only addresses immediate project needs but also fosters long-term partnerships, enhancing both client satisfaction and retention. By leveraging advanced technological tools and establishing clear communication protocols, printing companies can deliver high-quality folder printing services efficiently and effectively.
Common Misconceptions About Folder Printing
There are a few long-standing misconceptions surrounding folder printing that often affect how clients perceive the process. Particularly, the beliefs regarding printing speed misconceptions, quality vs. speed, and turnaround time clarity are worth addressing to ensure a more informed and satisfying customer experience.
Does Faster Printing Mean Lower Quality?
One of the most prevalent misconceptions in folder printing is that increased speed compromises quality. This is a critical area of misunderstanding. With advances in technology, such as the capabilities demonstrated by the HP Indigo 12000 Digital Press, high-speed printing does not necessarily mean a drop in quality. This digital press can handle larger orders efficiently while covering 97% of Pantone’s nearly 1,900 unique colours, ensuring vibrant, high-quality prints at quicker rates.
Understanding Turnaround Times
Another area where clarity is often required is the turnaround times. Understanding the full scope of what goes into printing, from initial design to the final output, is crucial for setting realistic expectations. Each project involves several stages that can affect the overall timeline. For example, standard resolution for web designs is typically 72 dpi, while high-quality printing requires a minimum of 300 dpi. Adjustments and adaptations to these requirements can add to the turnaround time but are necessary for premium quality outputs.
Moreover, higher volumes often lead to better efficiency. Digital printing technology, as seen in printers like the HP Indigo, has evolved to manage substantial orders without compromising on quality, challenging the traditional view that digital printing is only suitable for short runs. This capability helps dispel the notion that faster production must inherently sacrifice standards.
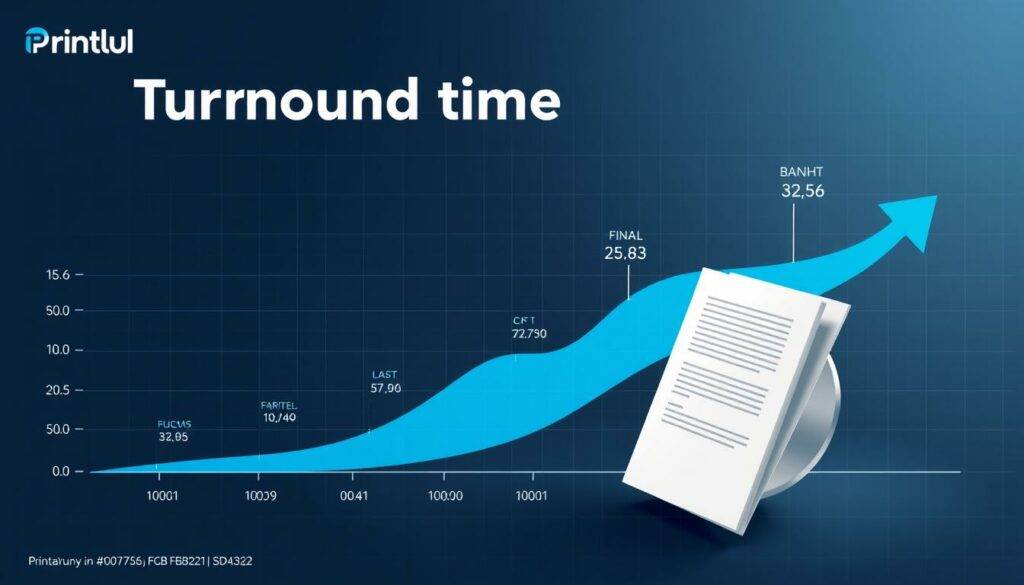
Overall, by debunking these printing speed misconceptions and providing turnaround time clarity, clients can approach their printing needs with realistic expectations and a clear understanding of the balance between quality vs. speed.
Getting Started with Folder Printing
Embarking on the journey of folder printing can be a highly beneficial endeavour for your enterprise. With presentation folders being a staple marketing tool in an array of business activities, from client pitches to events, their impact on branding and professional aesthetics cannot be overstated. As we move forward into 2025, the constant evolution of brochure design and the unyielding value of high-quality prints affirms the importance of starting folder printing with a reputable service provider.
How to Place Your Order at Printulu
Placing an order for presentation folders at Printulu is a customer-centric process, perfectly designed to accommodate the needs of all South African businesses and individuals. To get started, simply contact Printulu by phone or send your requirements via their support email address. The efficiency of ordering at Printulu ensures that your folders, whether they require intricate custom die-cuts, double-sided printing, or exclusive finishes like embossing, meet the highest standards of quality. With the approach of seasons filled with events such as Valentine’s Day or World Cancer Day, the need for timely and effective marketing materials is crystal clear.
Printulu is not just a placed with print service provider; it is equipped to handle the standard 9”x12” folders as well as custom projects that demand precise color-matching and a variety of coating options. Make an impression that lasts with custom printed presentation folders, joining the vast majority of businesses that leverage them for enhanced professionalism. From the robust, heavy-duty paper stocks to the eco-friendly options, Printulu provides the solutions that directly reflect your brand’s values and quality.
Visit Printulu’s website to discover the full product range and services on offer as you take the final step in ensuring your business materials stand out with optimal quality. With a user-friendly ordering system and the assurance of premium print results, your journey into the world of professional folder printing starts here.
FAQ
Why does folder printing take so long?
Folder printing involves a meticulous process that often results in longer production times due to quality control measures, complexities of design, and issues related to printing infrastructure. It’s a custom creation that requires careful planning and execution to meet expected standards. Therefore, patience is necessary for a high-quality final product.
What is folder printing?
Folder printing is the custom creation of folders used for business presentations or organisational purposes. The process includes designing the layout, selecting materials like the paper quality and finish, and employing various printing and finishing techniques.
What are the stages involved in folder printing production?
The stages in folder printing production include initial design conception, material selection, artwork preparation and approval, printing, finishing, and finally, quality control and proofing.
Why is precision in design so important for folder printing?
Precision in design is crucial as the folders must be both aesthetically pleasing and functionally effective. Accurate design ensures the final product aligns with the client’s vision and requirements.
How does material selection impact printing time?
The type of material selected can affect printing speeds, where different paper grades or coatings may require additional time to print or dry, influencing the overall production timeline.
How does print technology and equipment speed affect folder printing?
The speed and efficiency of print technology, like the type of printers and related equipment, are vital in the production timeline. Advanced technology can lead to faster printing times without sacrificing quality.
Does the volume of print jobs affect the speed of folder printing?
Yes, an increase in the volume of print jobs means that each job has to be queued and processed in order, which can lead to longer print times.
How does design complexity impact folder printing time?
Custom designs with detailed artwork require careful preparation and multiple iterations, which can significantly extend the time needed before the design is ready for printing.
Custom Designs vs. Standard Templates: Which is quicker?
Standard templates are quicker to process as they avoid the need for extensive customisation and usually have a faster artwork approval phase compared to custom designs.
What is the importance of proofing before final print?
Proofing is critical to ensure that the final printed folders match the intended design and quality. It allows clients to review and request revisions if necessary before the full print run is undertaken.
What are common reasons for production delays in folder printing?
Production delays can occur due to errors in printed samples, software and hardware malfunctions, such as ‘Access violation, WINSPOOL.DRV error’ or ‘Configuration Parser Error’, which may necessitate troubleshooting or restarting critical components.
How do coatings and finishes affect folder printing timelines?
Coatings and finishes, such as lamination or UV coating, may add to production time as these require additional processes and a curing period to ensure the quality of the final product.
Does the quantity of folders to be printed affect printing time?
Yes, small runs can be quicker but are less efficient, while bulk orders benefit from economies of scale but take longer to complete, especially when managing multiple designs within a single print run.
How do shipping options and their timeframes affect delivery?
Shipping options vary in delivery timeframes, with local delivery generally offering quicker turnaround compared to international shipping, which can face customs delays or logistical complexities.
What is the importance of timely communication in the folder printing process?
Timely communication between the client and the print service provider can streamline decision-making, facilitate quick changes, and address concerns promptly, ultimately reducing delays and improving efficiency.
Does faster printing necessarily mean lower quality?
Not necessarily. Advances in printing technology allow for faster printing times without compromising the quality of the finished folders.
How can I understand turnaround times better when it comes to folder printing?
Understanding turnaround times involves knowing the comprehensive processes each project goes through from design to delivery. This helps set realistic expectations about the timeframe for receiving high-quality printed folders.
How do I place my order for folder printing at Printulu?
To initiate folder printing at Printulu, customers in South Africa can contact them via phone at 010 593 0558 or email at [email protected]. Further details and product ranges can be found on their website at https://www.printulu.co.za.
Source Links
- Common Printing Issues and Ways to Solve Them – https://www.print-conductor.com/how-to/solve-common-printing-issues
- Why is print driver creating a folder everytime a user prints? – Microsoft Q&A – https://learn.microsoft.com/en-us/answers/questions/1344526/why-is-print-driver-creating-a-folder-everytime-a
- Presentation Folders 101: Guide to Custom Folder Printing – https://www.companyfolders.com/blog/complete-guide-to-custom-presentation-folders
- 5 Cardinal Rules of Presentation Folder Quality – https://www.printwand.com/blog/5-cardinal-rules-of-presentation-folder-quality?srsltid=AfmBOorp2tEyHHUCPuTZEUgPqyFbx8brZo4TPYuH2cANjZghY35MLErr
- Quick Guide to Presentation Folder Design | Printivity – https://www.printivity.com/insights/2020/02/06/how-to-design-presentation-folders/?srsltid=AfmBOor5zRX6SGuanub7ye34h5gubcI3hjQxaEU73RKEeepO5sMBK8hg
- How to Make a Printer Print High Quality (Canon, Brother, etc.) – https://kelleycreate.com/which-factors-can-impact-print-quality-the-most/
- 3D Matter Tests Color, Speed, & More – 3D Printing Industry – https://3dprintingindustry.com/news/color-speed-temperature-and-age-how-do-these-factors-influence-the-outcome-57141/
- Print Resolution: Basics and Beyond – https://richardphotolab.com/blogs/post/print-resolution-basics-and-beyond?srsltid=AfmBOopQqimCiM7JpxaPGKfBGvr-u2GbuN1FtnDQTp6nizbRHu4bi5wX
- Keep your project structure simple! – https://codeopinion.com/keep-your-project-structure-simple/
- Organized SCSS Folder Structures for Design Systems – https://blog.prototypr.io/organized-scss-folder-structures-for-design-systems-ecb861f1522c
- Best Practices for Data Governance and Quality Assurance – https://onlinedegrees.scu.edu/media/blog/best-practices-for-data-governance-and-quality-assurance
- WorkClout – What is Quality Control and How Can You Improve It? – https://www.workclout.com/blog/what-is-quality-control-and-how-can-you-improve-it
- Flyers, Forms & Folders – What paper to use for the top 5 F’s? – https://printing.printulu.co.za/flyers-forms-folders-what-paper-to-use-for-the-top-5-fs/
- Custom A4 Presentation Folders full colour | Express Print South Africa, overnight printing, last minute printing, rush printing, urgent print services, express printing, fast turnaround printing, emergency printing, quick print solutions, same day printing, instant printing, immediate print service – https://expressprint.co.za/product/custom-a4-presentation-folders-full-colour/
- Affordable Top Quality Custom Folder Printing | PrintMagic – https://www.printmagic.com/folder-printing/?srsltid=AfmBOoronK5w67VzC4LoUjrLObxYa88bWx6Utzt16es7-SkVSO7GYNMd
- 63911_StandardCvr_Prep.indd – https://cdn-s3.sappi.com/s3fs-public/sappietc/Sappi-The-Standard-Prepress-Preparing-Files-For-Print.pdf
- Printing – The Complete Guide – https://printing.printulu.co.za/paper-grammage-guide/
- Document digitization in transportation, logistics, and supply chain – Adexin – https://adexin.com/blog/document-digitization/
- The Printing Process: Steps of Commercial Printing – https://sheerprintsolutions.com/blog/the-printing-process-about-the-stages-of-commercial-printing/
- Logistics and Transport – https://www.kyoceradocumentsolutions.co.uk/en/business-solutions/sectors/logistics-and-transport.html
- How can print designers collaborate more effectively with team members? – https://www.linkedin.com/advice/0/how-can-print-designers-collaborate-more-effectively
- How to Share Files with Colleagues and Clients – https://filestage.io/blog/how-to-share-files/
- 5 Common Print Myths Debunked – Printivity Insights – https://www.printivity.com/insights/2023/05/19/common-print-myths-debunked/?srsltid=AfmBOoq9oTC-0B2-0eIFRYQalGV0M569eYqwV_6p65ftSXLxWFhoKEwD
- Dispelling Misconceptions About Digital Printing – % – https://www.xerocopy.com/2022/02/17/dispelling-myths-about-digital-printing/
- Presentation Folder Printing | Design and Print Services | Jetline – https://www.jetline.co.za/services/presentation-folders/
- Quick Guide to Presentation Folder Design | Printivity – https://www.printivity.com/insights/2020/02/06/how-to-design-presentation-folders/?srsltid=AfmBOorKFKNw0Bd6sejHLlxXkzXg8uyXWw4d9mul1c3c3MQSou435NYp
- Presentation Folders – 24Media – https://24media.co.za/product/presentation-folders/