Printing is an essential part of various industries, including textiles, advertising, and manufacturing. However there are so many different printing methods out there, that it’s really hard to understand what print technique goes with which product. Not to worry, we have you covered with our basic descriptions and handy go-to comparison. There are several types of printing processes available. Each with its own unique advantages and disadvantages. In this post, we will discuss seven different printing types and how they differ, most importantly what method goes with which product.
When it comes to printing, there are two main types to consider: digital printing and offset printing. Digital printing is ideal for small print runs and offers quick turnaround times, while offset printing is better for larger quantities and provides high-quality, consistent results. Both methods have their own unique advantages, so it’s important to consider your specific printing needs before making a decision. Whether you’re looking for cost-effective options or superior print quality, understanding the differences between these two types of printing can help you make the right choice for your project.
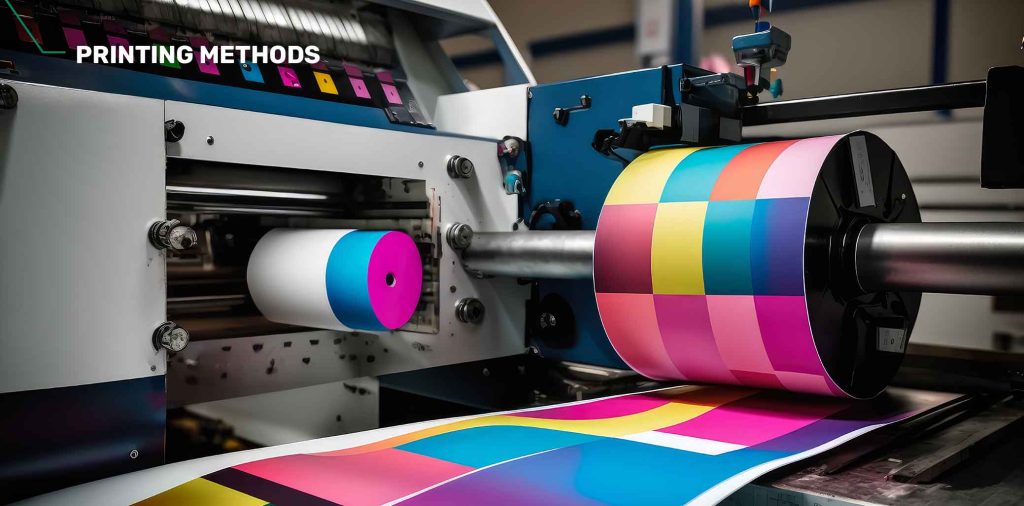
Types of Printing:
Litho Printing: (Cost Effective for High Volume Paper Printing)
Screen Printing: (Cost Effective Low & High Volume Printing)
Pad Printing: (Lower Volume Textiles & Brandable Items)
Dye Sublimation Printing: (Generally Higher Volume Textiles & Brandable Items)
Letterpress Printing: (Specialised Printing)
LED UV Printing: (Long Lasting Printing)
Flexography Printing: (High Volume Label Printing)
Digital Printing (Low Volume Label & Paper Printing)
Large Format Digital Printing (Low to High Volume Printing)
Direct to Film: DTF (Low to Medium Volume Printing)
Direct to Garment: DTG (Low Volume Printing)
Gravure Printing (Low to High Volume Printing)
When it comes to types of printing, there are several options to consider. From traditional offset printing to modern digital printing, each method has its own unique advantages and applications. Offset printing is great for high-volume projects and ensures consistent, high-quality results, while digital printing offers quick turnaround times and the ability to personalise each print. Additionally, there are speciality printing techniques such as screen printing and letterpress, which are perfect for creating tactile, visually striking prints. Understanding the different types of printing available can help you choose the best method for your specific needs.
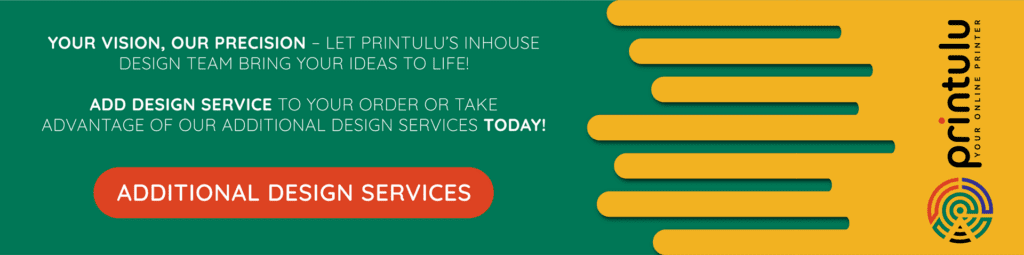
Litho Printing: (Cost Effective for High Volume Paper Printing)
Litho printing, short for lithography printing, is a high-quality and versatile printing technique that uses the principles of oil and water repulsion to create sharp, detailed, and consistent prints. It involves transferring ink from a printing plate (usually made of aluminium or other materials) onto a rubber roller, which then transfers the ink onto the printing surface, typically paper.
Litho printing excels in reproducing intricate designs, photographs, and vibrant colours, making it a popular choice for various commercial printing applications, such as brochures, posters, and packaging. Its precision and ability to maintain image quality over long print runs make it a reliable choice for large-scale printing projects.
The best artwork format for litho printing is typically high-resolution vector artwork from Adobe Illustrator or a similar vector graphics program. Lithography is a printing process that excels at reproducing intricate details and vibrant colours, and vector graphics are ideal for maintaining the highest quality in print.
Here are the key considerations for preparing artwork for litho printing:
- Vector Graphics: Vector graphics are composed of mathematical paths and curves rather than pixels. They can be scaled to any size without loss of quality, making them ideal for litho printing. Common vector file formats include Adobe Illustrator (AI), EPS (Encapsulated PostScript), and PDF (Portable Document Format) with vector elements.
- Resolution: If you need to include raster (bitmap) images within your artwork, make sure they have a high resolution (300 dots per inch or more) to ensure sharp and clear printing. These images should be embedded in your vector file.
- Colour Mode: Use the CMYK colour mode for your artwork. Litho printing typically uses the four-colour process (Cyan, Magenta, Yellow, and Key/Black), so CMYK design ensures accurate colour reproduction. Avoid using RGB colours as they are for screen displays and may will translate accurately to print.
- File Format: Provide your artwork to the printer in the requested file format, often PDF for litho printing. Be sure to follow the printer’s specific file submission guidelines.
Remember that the best practices for artwork preparation may vary depending on the specific requirements of your litho printing project and the capabilities of the printing facility you are working with. It’s always a good practice to consult with your printer and adhere to their guidelines for optimal results.
Digital Printing (Low Volume Label & Paper Printing)
Digital printing is a modern printing technique that involves using digital files to print images or text. This method uses digital printing presses, which can produce high-quality prints with excellent colour accuracy and consistency. Digital printing is often preferred for small to medium print runs. It offers fast turnaround times and does not require the creation of expensive printing plates. It is commonly used for printing marketing materials, packaging, labels, and personalised items.
The world of printing is vast and diverse, with each type of printing offering unique advantages and disadvantages. From screen printing to digital printing, there are a plethora of options to choose from depending on your printing needs. Whether you need to print on plastics, metals, or paper, there is a printing method that can accommodate your requirements. By understanding the differences between the types of printing, you can make an informed decision and achieve the best results.
For small format or digital printing, the best artwork format depends on the specific requirements of your project and the capabilities of the digital printer you’re using.
Key considerations for preparing artwork for small format and digital printing:
- Graphics: Vector or Raster graphics are composed of mathematical paths and curves rather than pixels.
- Resolution: 300 dpi (dots per inch) or more to ensure sharp and clear printing. These images should be embedded in your vector file.
- Colour Mode: CMYK colour mode
- File Format: PDF, Can be raster or Vector-based.
Remember that digital printing is not as crisp as litho printing.
Large Format Digital Printing (Low to High Volume Printing)
Large-format digital printing is a modern printing technique that uses digital technology to produce large-scale prints on various substrates, such as banners, posters, signage, and vehicle graphics. This method offers exceptional flexibility and precision, allowing for high-resolution and colourful reproductions of graphics, photographs, and text on oversized materials. Large-format digital printing is widely used in advertising, marketing, and visual communication industries to create eye-catching displays and promotional materials that can effectively convey messages and capture attention in both indoor and outdoor settings. Its versatility and ability to produce stunning visuals make it a popular choice for a wide range of applications.
For large-format printing, especially when dealing with graphics, you’ll want to ensure the best quality and clarity in your artwork. Here are the specifications for the best artwork format:
Graphics: Most likely Vector and Raster graphics.
Resolution: 200 DPI (dots per inch) or more to ensure sharp and clear printing. These images should be embedded in your vector file.
Colour Mode: CMYK colour mode for accurate colour reproduction in large format printing.
File Format: PDF, Can be raster or vector-based.
Additional Tips from an Ex Large Format Print Manager:
- View your final print at 100% to see the Print Quality.
- When looking at the print artwork – View it by standing 3 meters away. Remember most Large-format print products are not viewed up close.
- Use big font sizes and minimal words – Try to communicate visually
- Design with high contrast, otherwise everything just melts together.
- Add a blur to images that are pixelating to hide the pixelation.
Large Format LED UV Printing: (Long Lasting Printing)
LED UV printing is a printing technique that involves using ultraviolet (UV) light to cure ink onto a substrate. The ink is exposed to UV light, which causes it to harden and adhere to the substrate.
LED UV printing is mostly used for printing on plastics, metals, and other materials. LED UV printing offers a high level of durability. The ink does not require drying time, resulting in faster production times. This process replaces the process of vinyl adherence to surfaces.
Additional Tips:
- Small details will not print
- Longer Lasting Large Format print solution
- The alternative solution is to add UV Lamination, only to a vinyl print.
- For fine-detail vinyl sticker printing that doesn’t need to last long, you do not have to use UV printing.
Dye Sublimation Printing: (Generally Higher Volume Textiles & Brandable Items)
Sublimation printing is a process that involves transferring a design onto a substrate using heat and pressure. The design prints onto a special transfer paper using dye-sublimation inks. Then the transfer paper is placed onto the substrate and subjected to heat and pressure.
Sublimation is commonly for printing designs onto fabrics, such as t-shirts, hats, and bags. It can also print mugs, phone cases, and other promotional items. Sublimation printing offers a high level of vibrancy and durability. The design becomes a part of the fabric or substrate resulting in a long-lasting print.
Dye sublimation printing is a versatile printing method that can work with both raster and vector-based artwork formats. Here’s the best artwork format for dye sublimation printing:
Format: PDF
Compatibility: Can be Raster or Vector-based
For dye sublimation printing, you have the flexibility to use either raster or vector-based artwork, depending on your design and preferences:
- Raster-Based Artwork (High-Resolution Images):
- Use high-resolution images with a minimum resolution of 300 DPI (dots per inch) to ensure sharp and clear printing.
- Save your raster-based artwork in a PDF format to preserve image quality.
- Vector-Based Artwork (Illustrations and Graphics):
- Create vector-based artwork using software like Adobe Illustrator or CorelDRAW.
- Vector graphics are ideal for designs with sharp lines, text, and logos, as they can scale to any size without loss of quality.
- Save your vector-based artwork in a PDF format, and ensure that you embed your fonts or convert it to outlines.
When preparing your artwork for dye sublimation printing, keep in mind that there are colours that
Pad Printing: (Lower Volume Textiles & Brandable Items)
Pad printing is a printing technique that involves the use of a silicone pad to transfer ink onto a substrate. The silicone pad is the shape of the design that will print, it picks up ink from a plate.
Pad printing is commonly used to print designs onto 3D objects, such as promotional items, toys, and electronic devices. It can also be used to print on flat surfaces, such as paper and plastics. Pad printing offers a high level of precision, and it can print on surfaces that are difficult to print using other methods.
Here are the specifications for the best artwork format:
Graphics: Preferably vector graphics only.
Resolution: For raster graphics (such as images), use a minimum resolution of 300 DPI (dots per inch) or more to ensure sharp and clear printing. These high-resolution images should be embedded in your vector file if they are part of your design.
Colour Mode: Use the CMYK colour mode for accurate colour reproduction in pad printing.
File Format: PDF is a suitable format for pad printing.
Flexography Printing: (High Volume Label Printing)
Flexography printing is a printing technique that involves using a flexible printing plate to transfer ink onto a substrate. The printing plate is made of rubber, and the ink transfers onto the substrate using a rotating cylinder.
Flexography printing is commonly used for printing on packaging materials, such as cardboard boxes and plastic bags. It can also be used for printing on labels and other promotional materials.
Here are the specifications for the best artwork format:
Graphics: Both vector and raster graphics can be used for flexo printing.
Resolution: For raster graphics (such as images), use a minimum resolution of 300 DPI (dots per inch) or more to ensure sharp and clear printing. These high-resolution images should be embedded in your vector file if they are part of your design.
Colour Mode: Use the CMYK colour mode for accurate colour reproduction in flexo printing.
File Format: PDF is a suitable format for flexo printing, and it can contain both raster and vector-based elements.
Additional:
Die Lines and Cut Paths: If your design requires custom shapes or die-cutting, provide the necessary die lines and cut paths in your artwork.
Screen Printing: (Cost Effective Low & High Volume Printing)
Screen printing is a printing technique that involves the use of a mesh screen to transfer ink onto a substrate. The mesh screen is prepared by coating it with a photosensitive emulsion, which is then exposed to UV light to create a stencil. The stencil acts as a barrier, allowing ink to pass through only the open areas of the screen.
Screen printing is commonly used to print designs onto t-shirts, posters, and other fabrics. It can also be used for printing on paper, plastics, and metals. Screen printing offers a high level of durability, and the ink can be layered to create more complex designs.
The best artwork format for screen printing:
Graphics: Preferably vector graphics.
Colour Mode: Use the CMYK colour mode for accurate colour reproduction in screen printing.
File Format: PDF
Vector files such as AI, PDF, EPS, SVG, and CDR are the best file types to send for screen printing logos and digital artwork, be sure to save it as a PDF. Bitmap/Raster files such as PSD, TIFF, PNG, and JPEG are good to use when they are saved at a high resolution of 300 dpi or higher and look good at 100% view.
Gravure Printing (Low to High Volume Printing)
Gravure printing is a high-speed, high-quality printing process that uses engraved cylinders to transfer ink onto various substrates like paper, plastic, or metal. It excels in reproducing fine details and continuous-tone images, making it ideal for applications like high-end magazines, packaging, and decorative materials. Gravure’s distinct advantage lies in its ability to produce consistent and vibrant colours, making it a preferred choice for projects where image quality and print durability are paramount.
To ensure the best results in gravure printing, you should follow these specifications:
Graphics: Both vector and raster graphics can be used for gravure printing.
Resolution: For raster graphics (such as images), use a minimum resolution of 300 DPI (dots per inch) or more to ensure sharp and clear printing. These high-resolution images should be embedded in your vector file if they are part of your design.
Colour Mode: Use the CMYK colour mode for accurate colour reproduction in gravure printing.
File Format: PDF is a suitable format for gravure printing, and it can contain both raster and vector-based elements.
Here are some additional considerations:
- Vector Elements: If you have vector elements in your design (e.g., text, logos, illustrations), create them using vector software like Adobe Illustrator or CorelDRAW. Vector graphics are ideal for maintaining sharpness and clarity, especially for text and logos.
- Raster Images: If your design includes high-resolution images or photographs (raster graphics), make sure they meet the minimum 300 DPI requirement. Embed these images in your PDF file for printing.
Gravure printing can accommodate inks that are water-based where as Litho printing uses inks that are oil-based.
Creating the engraved cylinders for gravure is a more expensive setup that creating litho printing plates.
Difference between Litho & Gravure Printing
Letterpress Printing: (Specialised Printing)
Letterpress printing is a technique that involves using a press to press ink onto a substrate using a raised surface, such as a type of metal. The ink transfers from the raised surface to the substrate, leaving an impression behind.
Letterpress printing is for printing on paper. Often used for printing wedding invitations and other high-end printed materials. Letterpress printing offers a high level of texture, and it often creates a vintage look. This form of printing is highly artistic and adds to the exclusivity of the products or events.
The best artwork format for letterpress printing to create the blocks:
Graphics: Vector graphics.
Colour Mode: Use CMYK colour, B & W Setup.
File Format: PDF is a suitable format for letterpress printing, and it can contain both raster and vector-based elements.
Direct to Film: DTF (Low to Medium Volume Printing)
Direct-to-film (DTF) printing is a modern digital printing method that involves directly applying ink onto a transparent or semi-transparent film substrate. This process is for the creation of high-quality film positives or negatives for screen printing, flexography, and other analogue printing processes. DTF printing offers precision and convenience, allowing for the accurate reproduction of intricate designs and detailed graphics on the film, making it a valuable tool in the production of various printed materials, from T-shirt designs to labels and packaging.
To prepare artwork for DTF printing, follow these specifications:
Graphics: Both vector and raster graphics for DTF printing, depending on your design needs.
Resolution: For raster graphics (such as images), use a minimum resolution of 300 DPI (dots per inch) or more to ensure sharp and clear printing. If you are embedding raster images in your design, ensure they meet this resolution requirement.
Colour Mode: Use the CMYK colour mode for accurate colour reproduction in DTF printing.
File Format: PDF is a suitable format for DTF printing, and it can contain both raster and vector-based elements.
Direct to Garment: DTG (Low Volume Printing)
Direct-to-garment (DTG) printing is a digital printing method that directly applies water-based ink onto textiles, such as T-shirts, hoodies, and fabric items. This process is especially for producing vibrant and detailed designs on garments. DTG technology is versatile, allowing for full-colour and high-resolution prints without the need for screens or elaborate setups, making it ideal for custom apparel, personalised merchandise, and short print runs. It offers a quick and efficient way to bring complex and colourful designs to life on clothing, catering to the demands of modern fashion and customisation markets.
To prepare artwork for DTG printing, follow these specifications:
Graphics: Both vector and raster graphics for DTG printing, depending on your design needs.
Resolution: For raster graphics (such as images), use a minimum resolution of 300 DPI (dots per inch) or more to ensure sharp and clear printing. If you are embedding raster images in your design, ensure they meet this resolution requirement.
Colour Mode: Use the CMYK colour mode for accurate colour reproduction in DTG printing.
File Format: PDF is a suitable format for DTG printing, and it can contain both raster and vector-based elements.
Read More:
Your Full Guide To Large Format Printing