Printing flyers is a fantastic way to advertise your business or event. And when it comes to flyer printing techniques, offset printing is king! Offset printing offers high-quality results at an affordable price, making it a popular choice for many businesses. In this article, we will explore the ins and outs of offset printing and why it’s the go-to method for printing flyers.
Understanding the basics of offset printing
Before we delve into the world of offset printing, let’s take a step back and look at its history and evolution.
The history and evolution of offset printing
Offset printing has a rich history, starting way back in the late 19th century. It has come a long way since then, with technological advancements making the process more efficient and cost-effective.
One of the key milestones in the evolution of offset printing was the development of the offset press by Robert Barclay in 1875. This innovation revolutionised the printing industry by introducing a more efficient and reliable method of transferring inked images onto paper.
Today, offset printing involves transferring an inked image from a plate to a rubber blanket, which then applies the ink to the printing surface. This indirect method allows for consistent and high-quality prints.
Key components of an offset printing machine
An offset printing machine consists of several essential components that work together to produce outstanding flyers. These include the printing plate, the blanket, the impression cylinder, and the ink rollers.
The printing plate is a crucial element in the offset printing process. It is usually made of aluminium and is responsible for transferring the image onto the blanket. The blanket, typically made of rubber, then offsets the image onto the printing surface, ensuring a clean and precise print.
The offset printing process explained
Now that you have a basic understanding of offset printing let’s dive into the nitty-gritty of the printing process.
Offset printing, also known as lithography, is a widely used printing technique where the inked image is transferred from a plate to a rubber blanket, then to the printing surface. This process is based on the principle that oil and water do not mix, with the image to be printed receiving ink from ink rollers, while the non-image areas attract a film of water, keeping the non-image areas ink-free.
Preparing the design for offset printing
Before printing a single flyer, the design needs to be prepared. This involves setting up the artwork, proofing it for errors, and making any necessary adjustments. Skilled graphic designers ensure that the design is optimised for the offset printing process, taking into consideration factors such as colour separation, resolution, and the type of paper to be used.
The role of plates in offset printing
Plates play a vital role in offset printing. They are responsible for transferring the image onto the rubber blanket. The better the quality of the plates, the higher the print quality. Aluminium plates are commonly used in offset printing due to their durability and ability to hold fine details, ensuring a crisp and clear final print.
The ink and water process in offset printing
One of the unique aspects of offset printing is the ink and water process. In this process, the ink and water on the printing plate work together to create the final image. The ink adheres to the image area, while the water repels it from non-image areas. This delicate balance is crucial in achieving sharp and vibrant prints, with skilled press operators adjusting the ink and water levels to maintain the desired quality throughout the print run.
Advantages of using offset printing for flyers
There are several reasons why offset printing is the preferred choice for flyer printing. Let’s explore these advantages in detail.
Offset printing, a traditional printing method that has stood the test of time, offers a plethora of benefits that make it a top choice for producing flyers. The process involves transferring ink from a plate to a rubber blanket and then onto the printing surface. This meticulous technique results in unparalleled print quality, ensuring that your flyers are crisp, clear, and visually striking.
Quality and consistency in offset printing
Offset printing delivers exceptional print quality with sharp images and vibrant colours. The result is professional-looking flyers that are sure to grab attention.
Moreover, offset printing excels in providing consistency across all printed materials. Each flyer produced using this method will have the same high level of quality, ensuring that your branding remains uniform and impactful.
Cost-effectiveness of offset printing
When it comes to cost-effectiveness, offset printing shines. The more flyers you print, the lower the cost per unit. This makes it an ideal choice for large print runs.
Furthermore, the longevity of offset printing plates allows for high-volume production at a lower cost. This means that as your flyer quantity increases, the cost per flyer decreases, making offset printing a cost-efficient solution for mass distribution campaigns.
Versatility of offset printing
Offset printing allows for a wide range of options when it comes to paper types, sizes, and finishes. Whether you’re looking for glossy or matte, thick or thin, offset printing has got you covered.
Additionally, the versatility of offset printing extends to the ability to print on various paper sizes, from standard A4 to custom dimensions, giving you the flexibility to create flyers that stand out from the crowd. The wide selection of finishes available, including embossing, foiling, and spot UV, allows you to add a touch of sophistication and uniqueness to your flyers, making them truly memorable.
Potential challenges with offset printing
While offset printing has numerous advantages, there are a few challenges that you may encounter along the way.
Dealing with colour inaccuracies
Due to variations in printing equipment and materials, achieving exact colour accuracy can be a challenge. However, with proper communication and colour management techniques, these challenges can be mitigated.
Time constraints in offset printing
Offset printing may require more time than other printing methods, as it involves setting up the plates and making adjustments. However, the longer turnaround time is often worth it for the superior print quality.
Limitations of offset printing
Offset printing may not be suitable for every project. If you need a small print run or require quick turnaround times, digital printing may be a better option.
Despite these challenges, offset printing remains a popular choice for many businesses due to its high-quality results and cost-effectiveness in large print runs. One key advantage of offset printing is its ability to maintain consistent image quality throughout the print job, ensuring that each copy is virtually identical to the next.
Moreover, offset printing offers a wide range of paper options, from glossy to matte finishes, allowing for customisation to suit the specific needs of your project. This versatility in paper selection enables businesses to create unique marketing materials that stand out and leave a lasting impression on their target audience.
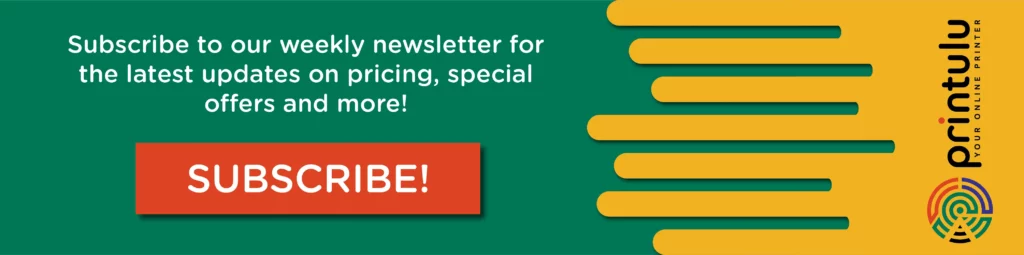